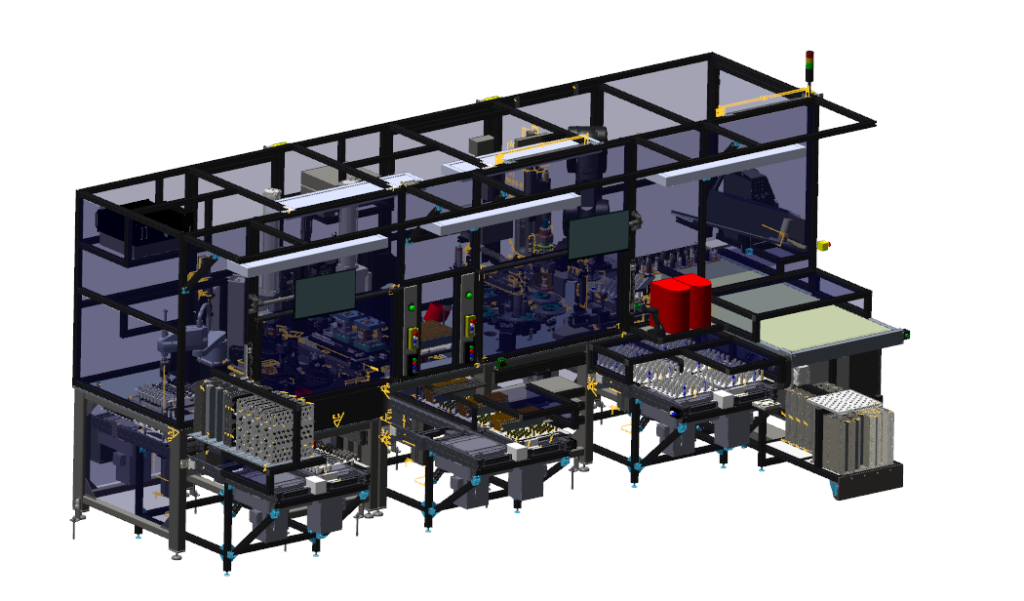
Over the past year, we worked on an outstanding project that involved building a three-robot, rotary table automatic press and assembly machine. The design and construction of the machine was a very complex task, as we had to overcome many challenges due to the huge product range.
We used Mitsubishi robots for the construction, which provide excellent quality and precise movement for the machine. We control the robots using a National Instruments controller, which allows for precise and fast operation of the machine. We used EtherCAT measurement devices for data collection, which allows us to monitor the machine’s operation on a continuous basis.
We collect data using Balluff IO-Link devices. IO-Link devices are a technology that allows for communication and data collection between system components. Balluff IO-Link devices are of excellent quality and reliability, and are easily integrated into the system.
During the construction of the machine, we used a new FESTO servo motor, which significantly increased the precision and speed of the machine. The biggest challenge was creating a new controller driver for the new motor, which took up a significant amount of time. However, we were able to complete the driver on time and integrate it into the machine, which allowed for optimal operation of the machine.
The completed machine is capable of automatically pressing and assembling products, which significantly increases productivity and reduces the possibility of errors.
We faced many difficulties during the construction, but we were finally able to build a machine that performs excellent quality and precise work. It’s a great pleasure for us that the machine is already in operation and generating profit for the customer.
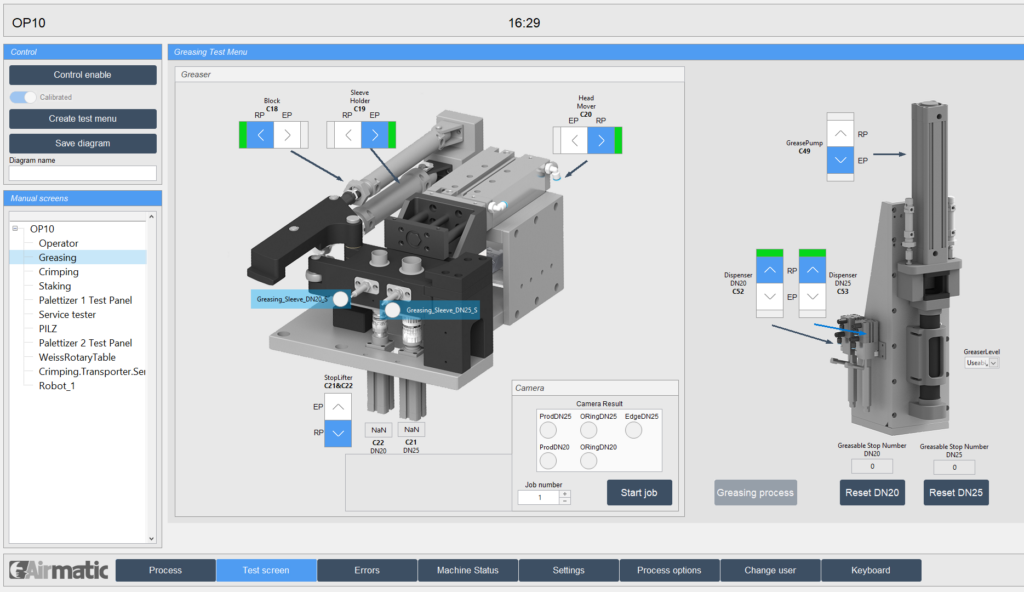
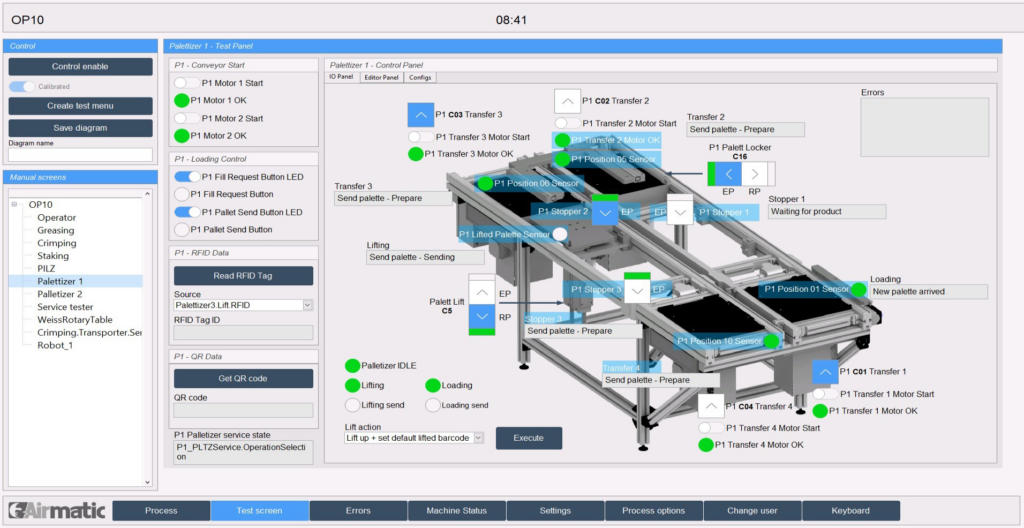
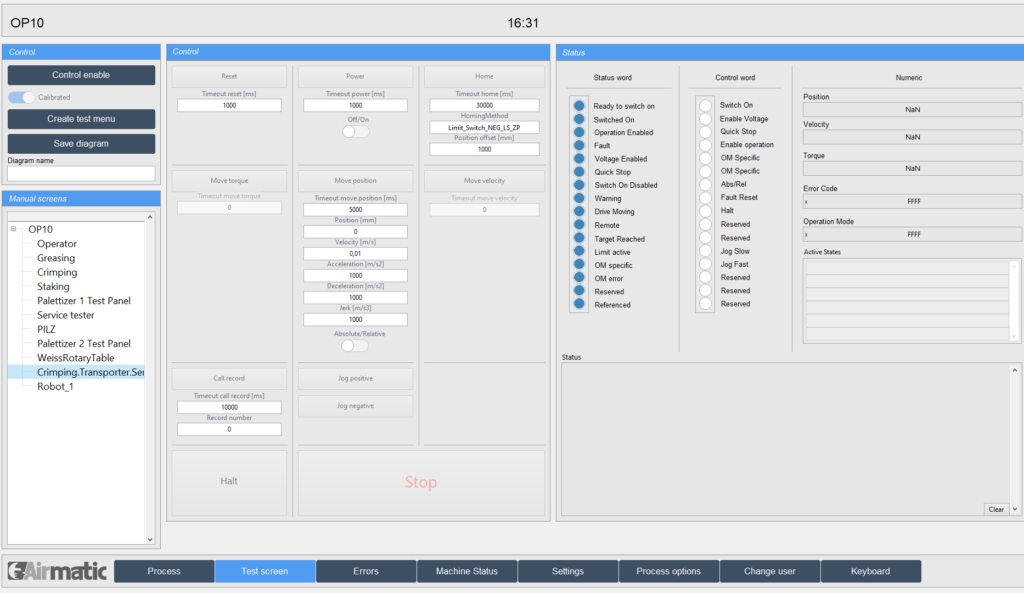